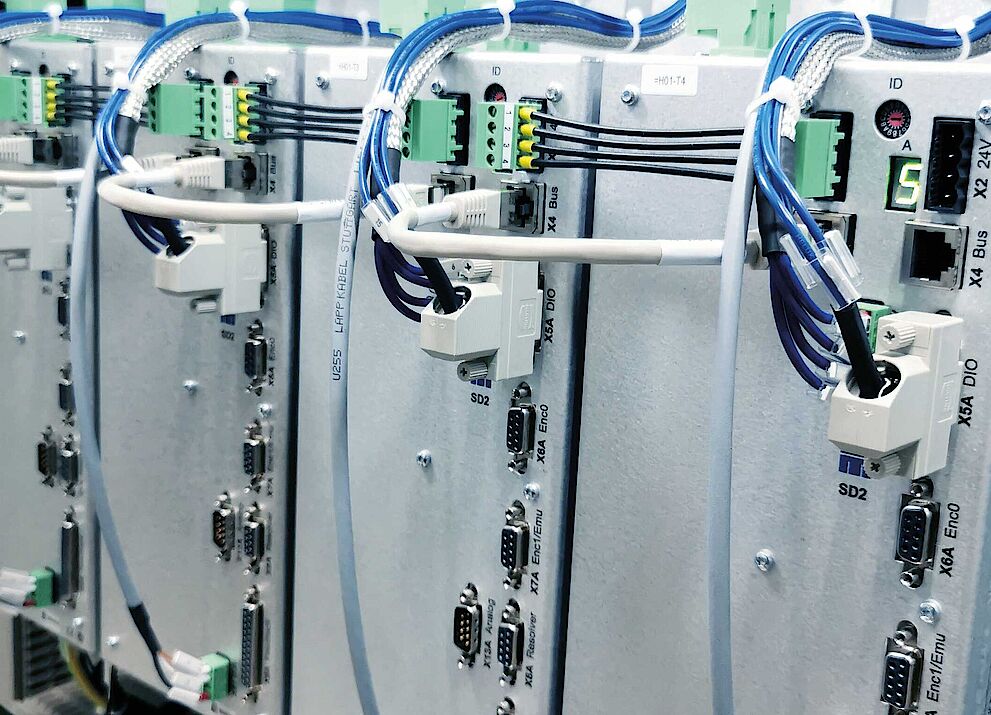
Technical papers
Numerous Advantages Through Device Replacement
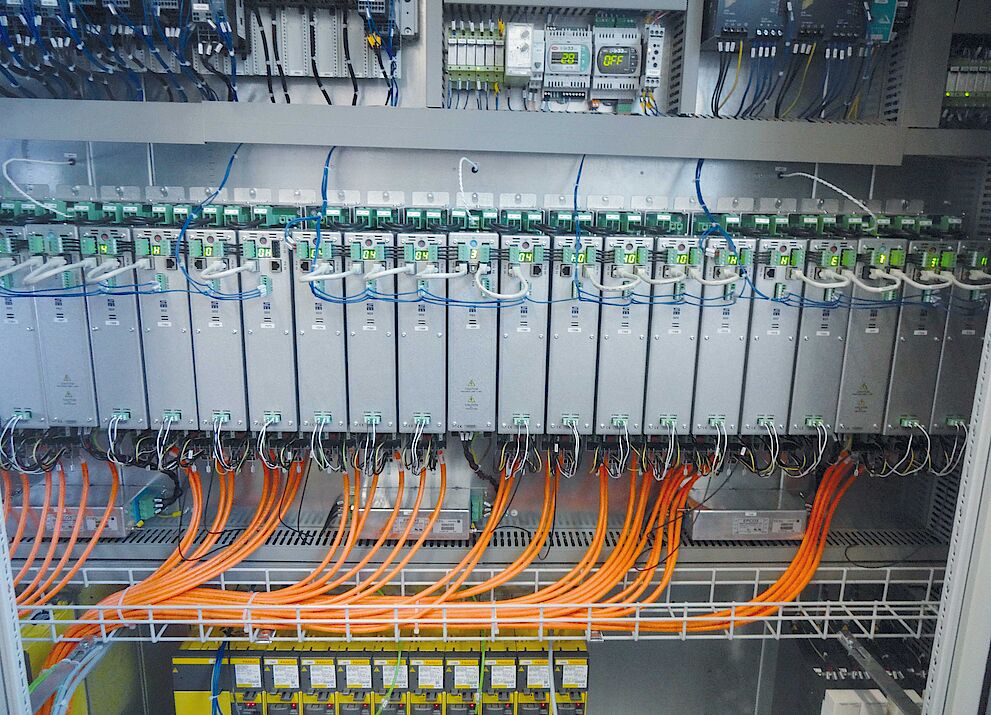
Technical papers
SIEB & MEYER High-speed Portfolio
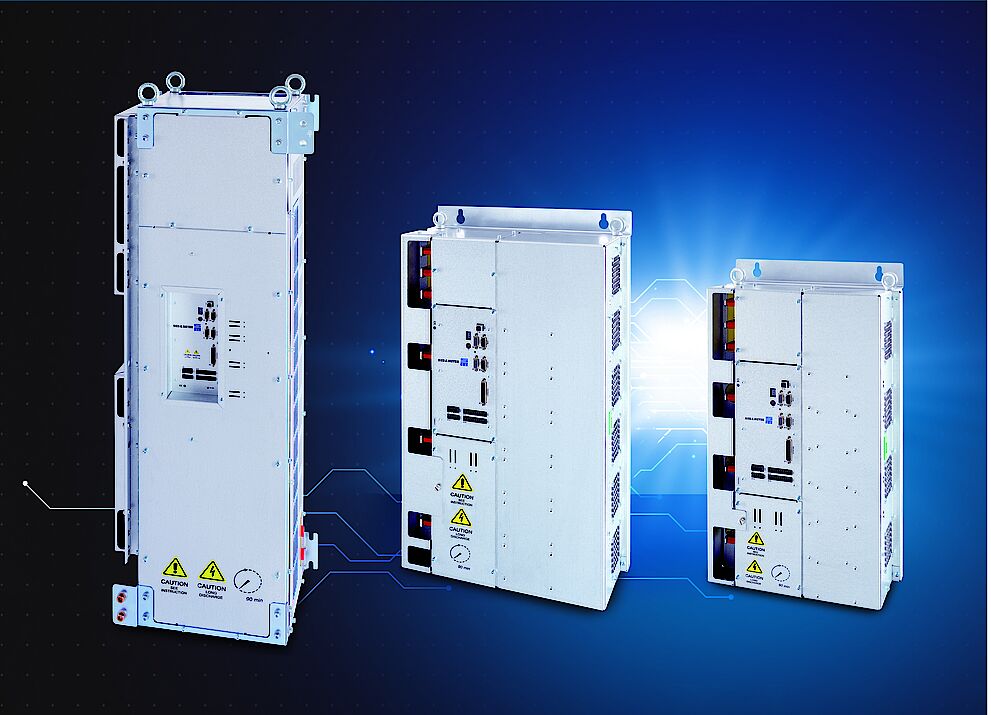
Technical papers
Efficient Driving of High-speed Motors
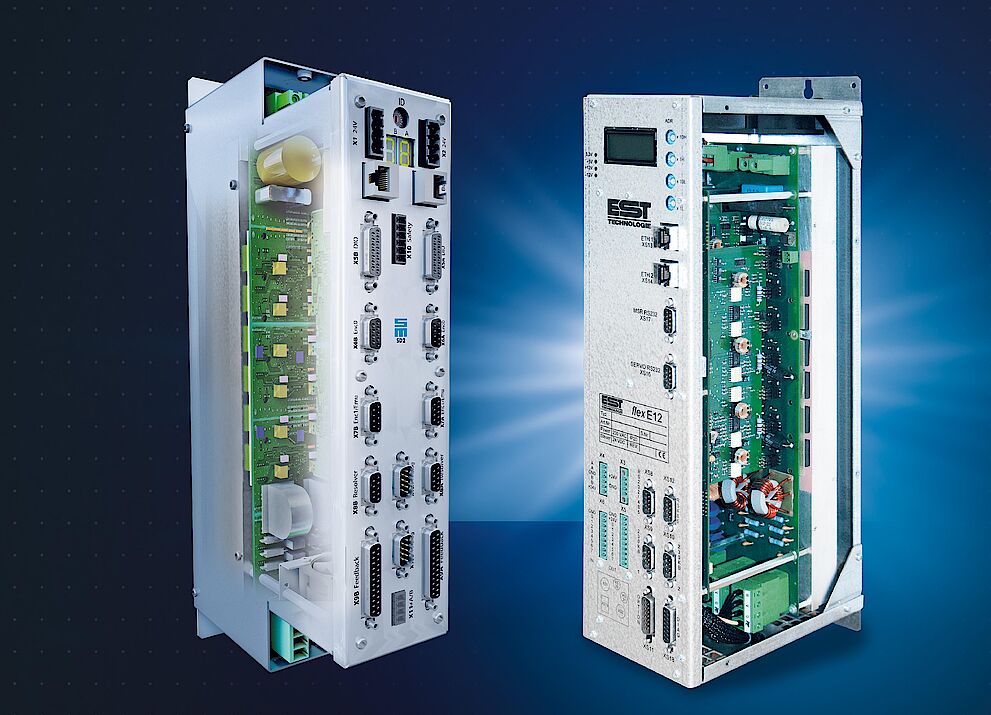
Technical papers
Long-term Benefits by Early Involvement
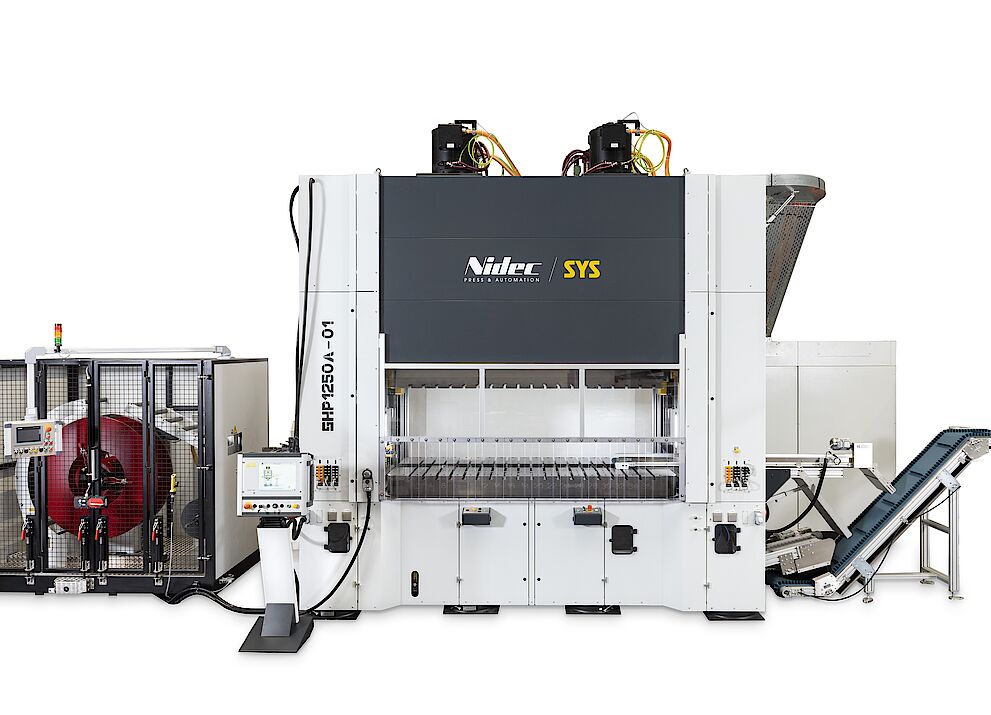
Technical papers
Precise Control of Servo Motors for Servo Stroke Presses
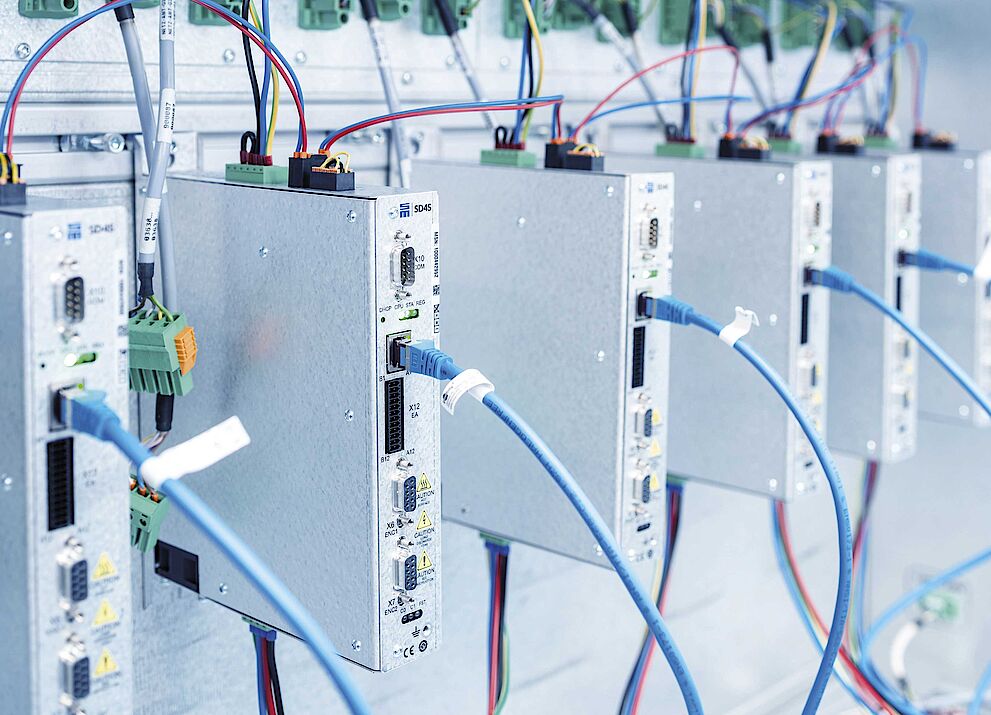
Technical papers
Screw Tightening with Straightforward Control
DO YOU NEED MORE INFORMATION?
If you have any further questions, please do not hesitate to contact our press department:
Ms. Annika Ritari
PR, Media and Exhibitions
Phone +49-(0)4131-203 - 1381
E-Mail Annika.Ritari @sieb-meyer.de
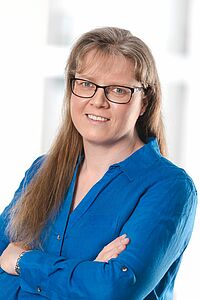