Efficient Driving of High-speed Motors
Technical papers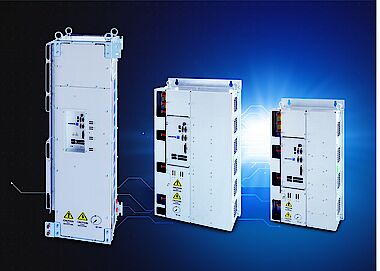
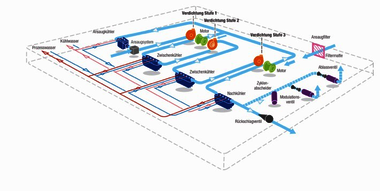
Three-level technology for a new turbo compressor
In the new turbo compressors by BOGE, the three-level technology of frequency converter SD2M by SIEB & MEYER can fully show its advantages. It ensures low rotor losses preventing excessive heating of the motor, which is extremely problematic in high-speed applications. Thanks to several, individual adaptations – for example a Modbus interface and optimized water cooling – the innovative frequency converter by SIEB & MEYER is the ideal solution for this sophisticated application.
BOGE is one of the leading global players in the field of compressors and compressed air systems. From food and plastics sector to steel and even pharmaceutical industry, numerous companies appreciate the high reliability, efficiency and economic viability of the various compressed air solutions. The portfolio ranges from individual compressors or compressed air components to complete system and service solutions. In the latter case, BOGE not only takes over the complete installation but also the inspection and maintenance of the system.
Three-stage compression
The BOGE product range of turbo compressors will shortly be extended by a 230 kW device. "Our turbo compressors save resources and energy. They can do without a drop of oil and reduce the noise level to a minimum despite the high speeds involved," described Peter Boldt, head of the turbo development at BOGE. "The low-wear turbo technology sets entirely new standards regarding efficiency and cost savings.
In the new 3-stage turbo compressors BOGE uses multilevel converters by SIEB & MEYER – specifically, the series SD2M with 150 kW and 75 kW. These frequency converters operate one or two permanent magnet DC motors in the compressors. Converter number one drives the compressor stages 1 and 2, converter number two drives the compressor stage 3. "The motors work with different speeds of about 35,000 or 55,000 revolutions each," said Peter Boldt. "By means of the interface to the compressor control, the speeds of the motors are synchronized to each other."
Efficient and cost-saving
The used drive technology is also highly efficient in other areas. Owing to the SIEB & MEYER frequency converters, the turbo compressors come with particularly compact dimensions. In contrast to competitive products, devices by SIEB & MEYER can do without motor LC filters or motor chokes, which are very large and heavy as well as costly and wiring-intensive. This reduces the footprint of the overall system. In addition, SIEB & MEYER integrated water cooling in the devices on the request of BOGE. Particularly important: thanks to the forward-looking converter technology, the overall efficiency of the turbo compressors was enhanced, resulting in lower energy costs. "We talk about savings of 3 to 5 percent," confirmed Peter Boldt. "That doesn't sound like much at first – but considering that the turbo compressor draws about 230 kW electrical power per hour, the users save a lot of money over the time.
For BOGE, however, the most important advantage of the SIEB & MEYER products is that these frequency converters were specially designed for high speeds. "Competitive devices may perform significantly worse in terms of efficiency and require more peripheral devices such as motor LC filters," emphasized Peter Boldt. "With SIEB & MEYER, our experience regarding converter efficiency has been very good, especially concerning the prevention of rotor losses, which is a crucial factor in high-speed applications."
Reducing motor losses
"This is exactly what our solutions are tailored to," confirmed Rolf Gerhardt, director sales drive electronics at SIEB & MEYER. "With our products, converter-based motor losses are significantly reduced compared to competitive products. Beside the lower motor heating, the system efficiency is increased and power consumption is reduced. This in turn saves costs – a win-win for the user." The background: about 90 % of all losses caused by the converter occur in the rotor. These losses result in heat that can damage the motor. Taking into account the small rotor volume as a design-specific factor of high-speed motors, further temperature problems are the outcome. The SD2x frequency converter family by SIEB & MEYER comes with control techniques that ensure a much smaller proportion of harmonic frequencies in the motor current
In comparison with the conventional two-level converter technology, the three-level technology used in the frequency converter SD2M goes even further: only half the voltage is supplied to the power semiconductors of the output stages. This makes the use of power semiconductor designed for much lower voltages possible. Better yet, these semiconductors can switch faster. The result: there are fewer switching losses in the output stage, which enables significantly higher switching frequencies. In addition, the motor is loaded with only 50 % of the voltage jumps compared to two-level technology. Three-level technology alone can reduce the losses generated in the rotor by about 75 %. If the switching frequency is also doubled, the losses in the rotor can be reduced by up to 90 %. Therefore, LC filters are often not required anymore – as in this application.
New technology on the horizon
So far so good – and it gets even better: BOGE plans additional turbo compressors for their product range that could be operated by devices from the new SD4x product family by SIEB & MEYER. The latter ensure operation of high-speed motors with even fewer losses. They also support PWM switching frequencies of 24 and 32 kHz. For an even finer modulation of the sine-wave signal, a commutation angle control for 32, 48 and 64 kHz is also integrated now. The result is an almost optimal sine with nearly no harmonic currents. Moreover, the power loss caused by the PWM can be reduced even further.