Precise routing for the perfect sound
Technical papers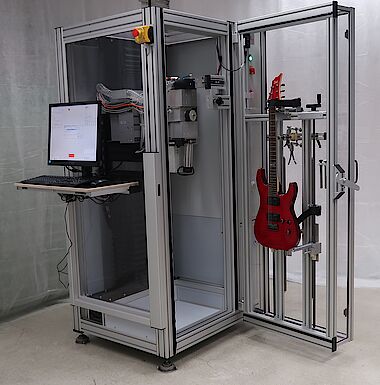
Frequency Converters in Multi-axis Machine Tools for Stringed Instruments
Making good stringed instruments even better: the German company A+D Gitarrentechnologie GmbH (Plek Berlin) achieves that with specially developed machine tools. The motors operating the routing spindles in these machines use the frequency converter SD2B plus by SIEB & MEYER as driver and amplifier. This converter with its compact design contributes to the optimal processing of the precious instruments.
A+D Gitarrentechnologie GmbH (Plek Berlin) is committed to guitar technology for highest demands. The Plek team aims at achieving the best possible playability of a guitar. For this purpose, special computer-controlled multi-axis machine tools are used. "We have developed these machines for this application only," explained Jens Baae, production manager at A+D Gitarrentechnologie GmbH (Plek Berlin). "The machine designs result from research and expertise gained over decades and a continuous dialog with guitar builders."
Modern technology for optimized playability
The machine tools are available in two designs: PlekPro and PlekStation. PlekStation is developed for service and can accommodate almost all types of fretted stringed instruments whereas PlekPro is optimized for the production. Though the latter comes with special adapters for each type of instrument, the complete process is automated, which shortens the processing times considerably compared with PlekStation.
The machines are used for scanning and processing guitars and similarly built stringed instruments like electric basses, electric guitars, acoustic guitars or mandolins. Primarily, the machines optimize the string action, i.e. the height of the strings from the fingerboard and the individual frets. "The string action differs depending on the instrument and preferences of the player," explained Jens Baae. "To determine the string action, the machine first scans the instrument under playing conditions – strung and tuned to pitch." A computer program determines the optimal values for each fret height as well as the height of the strings in the nut (top) and the saddle (bottom). In the following processing phase, the machine uses suitable cutter modules, e.g. a fret router and high-speed routing spindles, to put the determined values into practice. In addition, the high-speed routing spindles may be used for other processing steps, e.g. a complete rework of the fingerboard surface, pocket cutting of the fingerboard for inlays or recutting the slots for the frets in the fingerboard. When all processing steps are finished, the machine rescans the device to check that processing was successful.
Changeover to SIEB & MEYER drive
The high-speed routing spindles are operated by the frequency converter SD2B plus by SIEB & MEYER. However, this was not always the case: "At first, we used the power supply unit and amplifier from the manufacturer of the motor spindles but we were never one hundred percent satisfied with the performance," said Jens Baae. "When the manufacturer switched to a new device generation with different interfaces but without any real improvements, we looked for an alternative." Since the market of producer-independent motor controls for high-speed motors is limited, the choice fell quickly on SIEB & MEYER. "The SD2B plus fulfilled our requirements and after a test, it was clear that we will use this product," recounted Jens Baae.
SD2B plus is installed in the switch cabinet of the Plek machine. There are two types of high-speed spindles connected to SD2B plus. Each spindle type has an individual motor parameter set. During initial operation of the Plek machine, the parameter set is uploaded to SD2B plus via the parameterization and initial operation software drivemaster2 by SIEB & MEYER. "For processing, the SD2B plus operates the spindle motor, a PC program transmits the parameters via a serial interface to the SD2B plus," explained Jens Baae. "When the spindles are running, the PC reads the actual operating parameters, for example the actual current. In addition, the digital I/O interface transmits general machine states and commands."
SD2B plus: one device, many opportunities
SD2B plus is designed as high-dynamic servo amplifier for rotary and linear low-voltage servo motors, but also for the optimized operation of high-speed low-voltage synchronous and asynchronous motors. To allow as many applications as possible, the standard design of SD2B plus offers an optimum of maximum operating voltage and rated/peak current (80 VDC/10 A). Since 2020, SD2B plus is also available as high-current version, which achieves 30 % higher rated and peak currents with unchanged installation volume. The higher output current of 13 A significantly extends the application field of the device
"When used as frequency converter in high-speed applications, the SD2B plus permits control with sensors based on TTL encoders additionally to the control without sensors," explained Torsten Blankenburg, CTO at SIEB & MEYER AG. "This allows operation of several high-speed motors with angular synchronism via master/slave connection." The robust speed control can cope with high mass inertia ratios of up to 1:100 between motor and tool.
Compact, flexible and safe
SD2B plus comes in a compact IP20 housing with a height of just about 25 mm that makes the device especially suitable for small CAD/CAM routing machines. The safety function STO as well as an internal logic voltage supply are integrated. Beside two TTL encoder inputs and outputs, the device provides five digital inputs and five digital outputs as well as a USB interface for easy parameterization. A SERVOLINK interface allows operation with the SIEB & MEYER motion controller MC2 and the use of the fieldbus gateways for PROFIBUS, PROFINET and EtherCAT
Beside the compact dimensions and the support of the used motor type, for Plek the suitable interfaces and the safety functions were particularly relevant. "We were also convinced by the fact that SIEB & MEYER ensures perfect adaptation of the device to the motor type," Jens Baae pointed out. "The cooperation with SIEB & MEYER was good right from the start. Everything went very smoothly, from providing a test device to support for configuration and control as well as the creation of different motor profiles. We are quite satisfied."