Optimal Operation of IPM Motors
Technical papers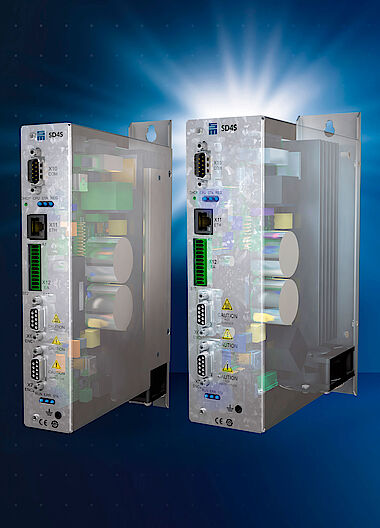
with frequency converters of the SD4x product family
The central advantages of the SD4x product family by SIEB & MEYER are optimized performance, higher speeds and low motor heating without additional sine-wave filters. In addition, SIEB & MEYER uses the now available processor performance for new control functions. As a result, SD4x devices can optimally operate synchronous motors with magnets embedded in the rotor, so-called interior permanent magnet motors (IPM motors).
Over the last decades, the permanent magnet synchronous motor with the magnets affixed to the rotor, also called SPM motor (surface permanent magnet motor), has replaced the asynchronous motor in many areas of automation. This development results from better characteristics regarding power density, efficiency, rotor temperature, max. torque and weight. A more recent development is the triumphant advance of the IPM motor. In contrast to the SPM motor, where the permanent magnets are attached to the rotor surface, this synchronous motor has the permanent magnets embedded inside the rotor.
Many advantages, more dependencies
Owing to its topology, the IPM motor – compared with the SPM motor – reaches a much higher motor inductance, which is quite advantageous for the operation with modern frequency converters. With the higher motor inductance, the frequency converter can, for example, better control the field weakening range (speed range with maximum available voltage), which is required for many applications. In addition, converter-based losses in the magnets are significantly reduced, resulting in a cooler rotor and higher efficiency
With an SPM motor, the two inductances important for the control, Ld and Lq, are almost the same and remain virtually constant over broad frequency and current ranges. This is quite different with IPM motors (Ld<Lq).
With an IPM motor, Ld and Lq are unequal, saturation-dependent and therefore not linear as well as variable depending on the motor current and also the frequency. In addition, the angle between the currents Id and Iq applied by the converter depends on the operating point.
Additional torque through unequal inductances
The inductance difference Ld<Lq has a topological advantage: with systematic slots in the rotor lamination, the motor generates additional torque for usage. When an external magnetic field is effective, the slots make sure that the rotor turns to the position with the highest magnetic conductibility. The additional torque is called reluctance torque. It is generated without increasing the phase current or magnets – 'free of charge' so to speak. In addition, this also saves expensive magnetic material. In order to utilize the reluctance torque, the following formula is applied:
M=m2p(ΨPMIq+Ld-LqIdIq
That means, an additional negative d-current (Id) is necessary, which results simply from distorting the phase current pointer (IS). By transforming the phase current pointer IS to orthogonal components, the currents Id and Iq can be calculated.
The negative inductance difference (Ld<Lq) and the negative d-current result in a positive torque. Thereby, current-related copper losses through the stator current IS are constant while the torque in the machine increases. With SPM motors, the current angle (outside the field weakening range) is always 90° because Lq=Ld
Compared to SPM motors, the control of IPM motors is much more complex for the frequency converter, though. The numerous dependencies in IPM motors can only be controlled and utilized when the motor manufacturer provides excellent, operating point-dependent motor data because identifying errors in the motor data is hardly or not possible at all due to the various dependencies between the individual parameters.
Motor manufacturers require control strategy
"For us as motor manufacturer it is essential that the operating point-dependent current angles of our IPM motors are optimally applied in the machine," explained Walter Schierl, product development manager at ATE Antriebstechnik und Entwicklungs GmbH & Co. KG – a company that has been working closely with SIEB & MEYER for many years. "This way, we want to achieve the maximum possible torque at every operating point with minimum losses for our customers." The reason: today's requirements for efficiency, installation space and torque density are only reachable when the machine is optimally supplied with current. "In this endeavor, new controller structures as provided by SIEB & MEYER products are the next imperative step in technology towards the future," said Walter Schierl
"To optimally control the IPM motor a clever strategy is required," confirmed Rolf Gerhardt, head of sales drive technology at SIEB & MEYER. "Only then, the motor reaches the maximum efficiency and torque at every operating point." Many standard converters make do with determining the required angle for the operating point at full load, which is also used for partial load operation. This, however, causes considerably increased motor currents and inaccurate current angles. The same torque requires too much phase current increasing the stator temperature. Alternatively, the generated torque is lower than the IPM motor could actually provide at this converter-set phase current.
Optimal conditions with converter series SD4S
"Another important factor is the dependency of the motor inductance on current and frequency," explained Rolf Gerhardt. "Particularly the inductances Ld and Lq are the focus here." Only when these dependencies are taken into consideration, the motor can reach optimal efficiency avoiding any inaccurate angles as well as unnecessary power loss.
The new converter series SD4S by SIEB & MEYER takes all requirements mentioned above into account. Using special control structures, SD4S converters can accurately determine the described dependencies and optimally control them at the respective operating point, which results in the optimal torque at lowest possible motor current (MTPA = maximum torque per ampere). Losses in the motor and in the converter are minimized. Beside improving the energy balance, this reduces the required amount of magnet material and also produces significantly lower CO2 emissions. The operating and parameterization software drivemaster4 – control center of the frequency converter family – provides all above-mentioned settings for the optimal operation of the IPM motor. "Our new control strategy enables motor manufacturers and users to optimally operate IPM motors," concluded Rolf Gerhardt. "So far this is very rare on the market."