Development history of a best-selling product
Technical papers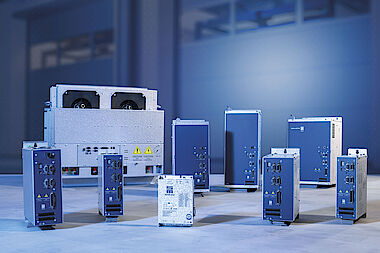
Frequency Converters: Past – Present – Future
At the end of the 1960s, the first series-produced frequency converters were launched on the market – and began their triumphant advance. Today they are widely used and indispensable for efficient operation of all types of motors. Naturally, the devices have evolved considerably over the 50-plus years: they have become more compact and light-weight, they use innovative materials and technologies and they come in numerous designs that cover different market segments and fulfill various requirements. The development is far from finished, though, since the wide spectrum of frequency converters still holds considerable potential for innovations.
Frequency converter – the term is widely known but also diffuse. Therefore, let´s begin with a simple definition: "Basically, the term frequency converter refers to an electronic device for driving motors at a variable speed," explained Rolf Gerhardt, head of sales drive technology at SIEB & MEYER AG. The German company based in Lueneburg develops and manufactures servo amplifiers and frequency converters since the beginning of the 1970s. Nowadays, SIEB & MEYER is a leading supplier of solutions for the high-speed sector.
The early days: rotary and static frequency converters
Originally, frequency converters were required because motors could only be operated with a fixed speed on the regular AC grid. In light of the progressive industrial automation, this was not sufficient anymore. New technologies were necessary to make an infinitely variable speed possible and simultaneously extend the speed range. "One evolution branch was the so-called rotary frequency converter, which essentially consisted of a higher-pole generator," Rolf Gerhardt imparted. "This frequency converter was coupled with a motor, usually two-pole, that was connected to the 50 Hz grid." Depending on the generator polarity, the resulting AC voltage at the generator output had a frequency higher than the grid frequency. With a 4-pole generator, the resulting output frequency was 100 Hz, which is max. 6,000 rpm. 6-pole designs could achieve 150 Hz (approx. 9,000 rpm). However, rotary converters were very complex, expensive and offered little flexibility – the drawbacks ultimately led to the extinction of this technology.
In the 1970s, the first static frequency converters came on the market; amongst them were products 'made in Lueneburg': in those days, SIEB & MEYER presented its first static frequency converters for high-speed spindles. "The technology of static frequency converters consists of power semiconductors and a semiconductor logic that controls the different functions," said Rolf Gerhardt. "The general functionality has not much changed until today." The converter rectifies the fix 50 Hz three-phase supply and converts the resulting DC voltage in the so-called output stages back into an AC voltage with variable amplitude and frequency, i.e the DC voltage is inverted. In theory, this technology can generate any output frequency and therefore speed; it also enables load-dependent tracking of the motor voltage and motor current.
Merging of servo amplifiers and frequency converters
Over a long period of time, the static frequency converters were divided into two product lines: one line for asynchronous motors required only for rotating (e.g. for drilling machines, conveyor belts, compressors or pumps) and another line for synchronous motors for positioning applications (e.g. robots and machine tools) – the latter was usually called servo amplifier. Frequency converters and servo amplifiers are actually based on the same power electronics with distinct logic and control technology. Until the beginning of the 2000s, SIEB & MEYER also separated the two product lines.
With the advent of increasingly faster processors and advanced power semiconductors, the classic servo drives and frequency converters were merged back into one device, which was often called just converter or drive amplifier. The software makes the difference: it adapts the device to the specific requirements and equips it for its future application. In addition, the dimensioning of the power electronics must be suitable for the rated to peak current ratio and furthermore some small additional modules might be necessary. Depending on the application, frequency converters are designed for high continuous power, whereas servo amplifiers are suited to dynamic load changes. "Our current product generations SD2x and SD4x can be used universally for both application fields," stated Rolf Gerhardt. "This is possible thanks to individual parameter settings."
Two-level converters for machine tools and the like
The basic construction of these devices is similar to standard 50 Hz converters: they provide passive rectification of the mains supply and come with fix DC link voltage or B6 IGBT output stage. For the operation of high-speed motors, though, the converters require faster switching power semiconductors in the output stage – this makes PWM frequencies up to 32 kHz possible. In addition, more accurate and faster current measurements as well as more powerful processor solutions are necessary. "In this application area, performance is more important than the price," Rolf Gerhardt pointed out. "With their control technology, our devices can drive asynchronous and synchronous motors with or without sensors in a speed range up to 240,000 rpm."
These motors operate, for example, machine tools with one or two processing spindles used for grinding and routing. Keeping the spindle heating as low as possible is especially important because it has a significant impact on the machining quality and the service life of the bearings.
In addition, the converters are used in turbo compressors/blowers with powers up to 30 kW. They usually operate sensorless synchronous motors with speeds up to ca. 180,000 rpm. With these high-speed motors, gears are not necessary, which leads to higher system efficiency. In this application area, high efficiency and low motor losses or low motor heating are also important factors.
The third level: for special applications
Three-level converters are the latest state-of-the-art converters. SIEB & MEYER provides the SD2M and SD4M devices with this technology. "Three-level output stage technology differs significantly in terms of costs and construction from two-level converters because twelve power semiconductors instead of six are necessary," explained Rolf Gerhardt. "This additional expense is only worthwhile in special applications." Then, the advantages are obvious: compared to two-level systems, the PWM losses are only 25 % with the same switching frequency. This reduces the motor losses significantly and expensive motor chokes or sine-wave filters are not necessary. Thanks to the 50 % smaller PWM switching amplitudes, the insulation stress of the motor winding is also reduced.
"Our three-level converters SD2M and SD4M can show their full potentials, for example, in the field of turbo compressors and turbo blowers," said Rolf Gerhardt. "On the one hand, these systems benefit from the low motor heating combined with the high system efficiency. With the 24/7 full load operation, the latter causes noticeable energy savings and short return on investment times. On the other hand, the overall system can be produced at lower costs and with a more compact construction volume because motor chokes and sine-wave filters are not necessary."
Quo vadis, frequency converter?
There is no foreseeable limit to converter technology in the future. At present, new large application fields open up, for example electromobility. In addition, new technologies like IPM (interior permanent magnet) motors enter the market. Although they require more control effort, these technologies can fulfill more requirements and enable using environmentally friendly and energy-saving technologies.
Moreover, the increasing variety of the application fields causes greater specialization of the frequency converters. Standard 50 Hz converters, for example, provide a simple closed-loop control of the speed at low costs. Their goal is to make the processes more flexible and increase the efficiency or save energy in systems that formerly ran without closed-loop control. "In this product area, we observe a trend towards higher circuit integration that results in lower costs," said Rolf Gerhardt. "In addition, the manufacturers use more and more IIoT (industrial internet of things) communication interfaces."
Further development of mobile and high-speed converters
High-speed converters for stationary applications, such as the products by SIEB & MEYER, allow the operation of motors with speeds up to 300,000 rpm. The focus of the devices is to keep the motor loss low during operation of these special motors and to achieve high system efficiency, for example, by omitting gears. Another reasonable approach is the use of advanced semiconductors based on SiC (silicon carbide) and GaN (gallium nitride) or multilevel topologies. Moreover, the converter development focuses also on the functional expansion, for example, integrated safety functions or fast, Ethernet based fieldbus and IIoT interfaces.
With frequency converters for mobile applications, a good efficiency and the mechanical properties are in the foreground – e.g. regarding dimensions, weight and robustness against challenging environmental conditions. Suitable power semiconductors help fulfilling these demands. Modern components based on SiC (silicon carbide) and GaN (gallium nitride) enable high switching frequencies with low switching losses.
"These examples show that the development potential in the field of frequency converters is far from exhausted," concluded Rolf Gerhardt. "The requirements for these devices will continue to change in the future and therefore demand ongoing development of the converter technology." The experts from Lueneburg show how this can be done: SIEB & MEYER has developed a device series based on the new development platform SD4x that is future-proof in every way. The devices support new interfaces and offer a number of additional functions. Users benefit from optimized performance, higher speeds as well as lower motor heating without sine-wave filters. The enhancements allow improving the production quality for existing applications and, beyond that, exploring completely new fields of application.