Consolidated Competence
Technical papers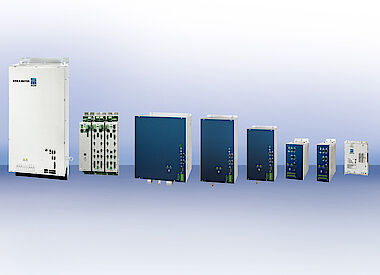
for Precise Dressing Processes
When two companies collaborate – both absolute experts in their respective fields – this results in high-quality products. Such a collaboration exists between the German companies DR. KAISER DIAMANTWERKZEUGE GmbH & Co. KG and SIEB & MEYER AG: the powerful dressing spindles made in Celle work especially precise and dynamic with high-performance frequency converters made in Lueneburg. The high level of expertise combined with a close collaboration of both companies guarantees best results in dressing applications especially for sensorless spindles, which means considerable added value for the end customers.
In 1977, Dr.-Ing. Michael Kaiser got started with his 'shop for diamond tools' and has consistently expanded the company over the following decades: today around 360 highly qualified employees work on the site in Celle and manufacture products in the fields of dressing tools, dressing spindle systems, wear resistant parts and grinding wheels. By now DR. KAISER is globally established as problem solver for all requests regarding 'the grinding zone'. "Our goal has always been to provide a complete solution for the customers' grinding and dressing applications," Dipl.-Ing. (FH) Stephan Grote, production manager for dressing spindle systems at DR. KAISER, pointed out. "Beside our vitrified bonded CBN and diamond grinding wheels, this applies particularly to our rotary diamond dressing tools. These are developed individually for the customer process."
Frequency converter for optimal running behavior
Ideally, the tools are mounted and precision-balanced on the suitable dressing spindles by DR. KAISER. The dressing spindles are usually equipped with high-frequency asynchronous motors that require special frequency converters to ensure optimal running behavior. The frequency converter is the link between dressing spindle and machine control. Beside controlling the dressing spindle, the frequency converter forwards relevant process data to the machine control. This is where SIEB & MEYER comes into play: depending on the individual application, DR. KAISER recommends customers to use different frequency converters of the device series SD2x. These frequency converters are optimized for high rotating field frequencies and ensure very low motor heating.
Exactly that is required for dressing applications, since it is essential to keep the spindle temperature low: a temperature increase in the spindle causes a longitudinal growth and therefore a shift of the tool position. This must be prevented. Frequency converters by SIEB & MEYER ensure constant spindle temperatures and can also dynamically control different load situations. For dressing very hard grinding wheels, the used frequency converters must also provide a high speed constancy and the maximum possible torque – factors where the devices by SIEB & MEYER convince all along the line. Stephan Grote said, "We as well as our end customers had very good experience in all aspects. The tests have optimal results time and again."
Working together for individual solutions
The decisive factor for an optimal implementation is the parameterization of the frequency converter. For this purpose, the SIEB & MEYER service team supports the experts at DR. KAISER: together the two partners optimize the characteristic curves of the individual spindle. With more than 400 different dressing spindles and over 50 different motor types, such a technical support is crucial. The geographical proximity of the two companies makes the support easier. If required, the employees of both companies can come together at short notice to work out a solution for the end customer. Although many issues might be solved via digital communication by now, a constructive teamwork on site has proven successful in many cases.
SVC control also for asynchronous motors
SIEB & MEYER has expanded the system software of the SD2x frequency converters with a SVC control for asynchronous motors to meet the requirements of customers like DR. KAISER. The reason: many dressing spindles are driven by asynchronous motors. These motors need to be controlled suitably. In addition, their speed must be constant in different load situations. "Sensorless vector control was used mainly for synchronous spindles until now," said Markus Finselberger, key account manager drive technology at SIEB & MEYER. "For asynchronous motors we also have a solution ready, which is meanwhile proven and established at DR. KAISER in particular for dressing with sensorless asynchronous spindles."
In this case a highly precise speed control is very important because the ratio of the circumferential speeds of diamond coated dressing rollers to the grinding wheel must be kept constant. This means that the dressing spindle speed may deviate only minimally from the set speed during operation. Particularly for synchronous dressing spindles with speed ratios of qd > 1, DR. KAISER recommends using integrated sin/cos encoders that enable a precise speed feedback to keep the speed constant even when greater forces take effect. Due to lack of space or for financial reasons, end customers frequently cannot integrate such a sensor. In these cases, DR. KAISER trusts in the sensorless vector control SVC provided by the SIEB & MEYER converters. An intelligent method determines the actual speed using measured current and output voltage values, which enables a speed control without speed sensor but with good performance. This control method has two essential advantages: the cost reduction on the one hand and the opportunity for the engineer to make the construction more compact on the other hand. When the space in the machine is small, the customer can use the construction space made available for other components.
Although DR. KAISER is very satisfied with the frequency converters of the series SD2x, the company looks forward to the launch of the next generation: at present, SIEB & MEYER develops the SD4x series that offers many improvements regarding power and equipment. "We are in close contact with the development department and we will definitely test the new devices," concluded Stephan Grote. "If the results are good, as we expect, we will include these frequency converters in our portfolio." The next step in a partnership that will celebrate success also in the future thanks to much know-how and commitment.