Three-level Technology Helps Avoiding Converter-based Power Losses
Technical papers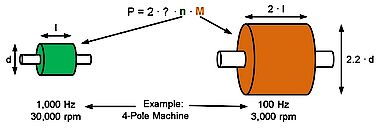
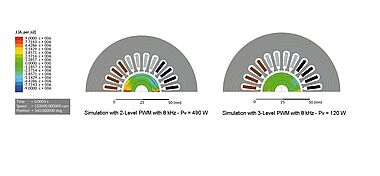
SD2M opens up new application areas for high-speed motors
The company ATE Antriebstechnik und Entwicklungs GmbH & Co. KG has often faced technical limits with regard to the realization of customized high-speed drive solutions: Extremly high speeds at compact dimensions were almost impossible due to high rotor losses. Without additional measures such as cost-intensive LC filters or active cooling, the motors overheated. The frequency converter SD2M by SIEB & MEYER solves this problem: Thanks to the three-level technology, converter-based power losses can be significantly reduced – which opens up entirely new possibilities for the drive specialist ATE.
For each customer the optimal electrical motor: ATE has specialized on high-efficiency electrical drive system for high speeds or frequencies that are individually designed for the specific application and its requirements. In this process, the experts also recommend the suitable frequency converter to their customers. "For our high-speed, permanent magnet motors, we are pleased to refer to the devices of our partner SIEB & MEYER", explained Dr.-Ing. Andreas Neubauer, Head of Development at ATE Antriebstechnik und Entwicklungs GmbH & Co. KG. "Especially, when we push the speed possibilities to their limits, an appropriate frequency converter is essential."
Frequency converters for high-speed drive systems
The frequency converters by SIEB & MEYER particularly make sense for the high-speed drives by ATE, which are deployed for example in turbo chargers or in the fuel cell ventilation. "Fuel cells are among others required in the e-mobility. Currently, we receive a lot of inquiries in this application field", said Andreas Neubauer. "The cells must be supplied with high oxygen volumes for the hydrogen combustion." The oxygen supply is realized via a high-speed compressor. With its motor frequencies of more than 1,600 - 2,400 Hz the compressor exactly fits one of the core competencies of ATE and SIEB & MEYER.
Electrically driven high-speed motors, however, are not only suitable for the above mentioned application fields – further application examples are the internal cylindrical grinding of high-precision ball bearings, the aluminum volume cutting of integral aircraft parts, the high-speed drilling in the PCB processing as well as turbo compressors resp. turbo blowers in the industrial production of compressed air. "In addition, there are many more application fields where higher speeds are required in order to enhance the processing quality or to reduce the production times", illustrated Rolf Gerhardt, Director Sales Drive Electronics at SIEB & MEYER. "Even if there is little space, high-speed motors are a good choice. In comparison to standard models, they feature an extremly small size and low weight."
Technical challenges of high-speed motors
Not only the high-speed motor itself but also its inductance is significantly smaller because of its physics. This fact makes it difficult for the current standard frequency converters with two-level pulse-width modulation to provide the motor with the required current quality. Due to the low inductance, significant harmonics in the motor current arise on the desired sine wave. This so-called ripple current causes nothing but losses in the motor, of which 90% occur in the rotor. Incurred by the small motor volume due to design restrictions, it is challenging to limit the rotor and shaft temperature to acceptable values.
To reduce the undesired harmonics, quite often filter components are connected between the converter and the motor – either so-called motor chokes (inductances) or LC filters that are composed of inductances and capacitors. Both solutions have clear disadvantages with regard to additional costs, additional installation space and weight as well as efficiency losses. Moreover, with LC filters, difficulties with regard to resonance frequencies often occur. If they are not designed with utmost care, they can cause major problems for converters and motors.
Three-level technology opens up new application fields
The best way is to not allow the desired harmonics to come up – or to reduce them to the value permissible for your individual application already at the point of origin, i.e. in the converter. "This can be guaranteed with our frequency converter SD2M, which is based on the three-level pulse-width modulation", explained Rolf Gerhardt. "It produces much higher current qualities, resulting in a significantly lower temperature in the motor."In a direct comparison - at the same PWM frequency - the converter-based additional rotor loesses are reduced by more than 80%.
In most of the cases, this is sufficient to entirely do without LC filters or motor chokes. SD2M comes with the innovative three-level technology designed for output powers up to 432 kVA and rotating field frequencies up to 2,000 Hz. As a basis for customized solutions, the company can implement individual customer soutions with motor currents up to 650 A – either equipped with air or with liquid cooling.
"The three-level technology is of great importance to us, because the rotor losses can be considerably reduced", stressed Andreas Neubauer. "In the past, we have often failed due to the high rotor losses during the implementation of customized projects. This is based on the fact that often active rotor cooling is not possible and that the heat convection brings only limited success." The three-level technology enables ATE to realize complex applications with high speeds and compact installation sizes – because heating is prevented beforehand. "In the past, in the above mentioned application as turbo blower for fuel cells, the technical limit was reached at approx. 20 kW. Now, 35 kW are a definitely conceivable value", specified Andreas Neubauer.
ATE does not need anymore to speculate in the planning phase about how warm the high-speed motor will get, because the experts use Motor Analyzer. SIEB & MEYER has developed this software for the dimensioning of drives considering the related converter. "The tool allows us to simulate the current form and to precalculate the portion of impure currents", concluded Andreas Neubauer. "Such specific calculations represent for us and for our customers a great added value."