Project Management in the Machine Tool Industry
Technical papers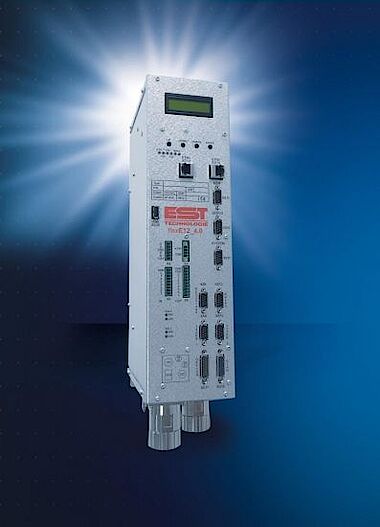
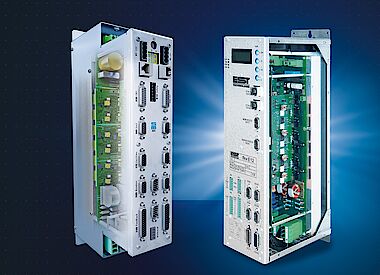
Step-by-step to the customized drive solution
SIEB & MEYER, the German specialist for drive and control technology, is the right partner for customized solutions. Among other things the customers benefit from the fact that SIEB & MEYER offers everything from one source: All steps from joint planning to serial production of the specific solution are realized in the company. This approach not only assures an efficient implementation, but also an optimal adjustment of the products regarding each customer's special demands – a literally "tailor-made" solution.
From simple hardware adjustments like special types of housing to completely new designed devices and features: SIEB & MEYER offers customized solutions in the field of high-speed frequency converters and servo amplifiers. Over 50 % of sales in the field of drive technology is generated by customized projects. The customized solutions are designed on the basis of SIEB & MEYER standard components that are successfully established in the market. In addition, SIEB & MEYER looks back on more than 50 years of experience from many customized drive systems that are produced in series quantities between 50 and 10,000 pieces.
Precise definition of requirements
To reach maximum innovation and flexibility SIEB & MEYER development teams work in close cooperation with the production team. What this looks like in concrete terms can be well explained using the example of a current project: Some years ago SIEB & MEYER developed a highly dynamic 2-channel servo amplifier for servo-driven tightening applications in the automotive industry for EST – based on the drive system SD2." The interesting thing about this project is that the customer himself has developed the control board or processor card of SD2", Ralph Sawallisch, key account manager for drive technology at SIEB & MEYER explained.” We designed the circuit for the device control of SD2, while our customer has integrated this circuit in its own layout." The drive system with an individual front end is well established in controls for tightening and press applications. Now, however, EST has connected a new generation of handheld tightening tools, which required implementation of an Ethernet interface. Accordingly, the partners had to jointly develop the processor card further.
"Once a customer demands a device that is not part of our standard portfolio, our internal process chain is activated", Ralph Sawallisch explained.
"This, of course, also applies for modifications of existing and possibly already customized devices like those for EST." The next step is a function test with a standard device. This is particularly important for new customers: They should gain confidence in the technical competence of SIEB & MEYER. Furthermore, such system tests reduce the risk for further development on a wrong basis. Since the tightening control was not yet available, a significant function test at EST was not possible, but also not necessary – after all, the customer had already gained long-time positive experience with power electronics by SIEB & MEYER.
Requirement specification – more safeness for the customer
In the next step, the customer writes a requirement specification. "For the customer it is much easier to specify his requirements on the basis of the experiences gained in practical tests", Ralph Sawallisch explained. "He can refer to existing technical developments and define additional features." Good requirement specifications facilitate the process for all involved partners: After all, these specifications include the requirements and can, if needed, be referred to again later. This is particularly important for time-consuming projects. This offers additional safeness particularly for new customers. However, if the requirement specification is too detailed, its realization may be difficult – since there is less scope left for the development by SIEB & MEYER. "The clear focus in the requirement specification of EST was on the description of the interface between the EST tightening control and the SIEB & MEYER-logic", Ralph Sawallisch explained. "The challenge was to unite them on one board."
The next step: effort assessment
Based on the requirement specification SIEB & MEYER makes a rough assessment of the work and time required and evaluates the sustainability of a project. Not only the feasibility plays an important role for example with regard to the capacities, but also the question whether SIEB & MEYER plans further development in the corresponding field. Last but not least, the scope of delivery plays a role: If the customer requires devices in great quantities over many years, the project will a priori be more profitable than smaller development projects, even if they offer a higher technical challenge. "Generally speaking, it is important to find out, whether this project is in line with all relevant aspects at SIEB & MEYER," Ralph Sawallisch explained. In case of a positive decision the development and management set a target price. By the way, pure engineering projects to be manufactured for example in China are always rejected. All customized devices by SIEB & MEYER are also on manufactured in Lueneburg.
Customer-friendly calculation
After the customer has agreed on the target price, a detailed assessment of the work and time required follows. The responsible developer for this step at SIEB & MEYER is Alfred Lemke. "When I receive the project definition, I look for equivalent parts in comparable already realized projects", the developer explained. "The more equivalent parts we can use, the shorter the time for development will be and better price conditions for the customer can be reached. When all details are cleared I start evaluating the time and material required." In the majority of cases, only a customer-friendly lump sum is calculated for the development of individual solutions. "Any vagueness often appearing during this phase is in favor of the customer". This was also the case in the EST project: The time required for the development was longer than planned – both partners underestimated the effort. Nevertheless, the partners found ways and means to bring the project to a good end.
Based on the detailed assessment for the work and time required the sales department prepares an individual quotation. After the approval of the customer SIEB & MEYER writes, if required, a functional specification – this service is part of the quotation and therefore subject to charge. In any cases, technical and chronological milestones are defined. The individual steps during the development are determined in cooporation with the customer. "In the case of the EST project the milestones were subdivided into many workings steps, because many partners worked on this project in parallel", Ralph Sawallisch remembered. "For the function tests all individual components had to be united. This required and still requires intensive exchange between the partners."
The development: A customized devices comes true.
Now, the project really starts: After all this essential preliminary work the development begins. "This is where magic happens", Ralph Sawallisch smiles. "Now, nearly all departments work in close cooperation to realize the project.” The electronics development designs the circuit diagrams, while the construction department works on the prototype of the device. During this phase, the manufacturing department, test field technicians and, last but not least, the technical documentation department are involved at an early stage. This requires active exchange between all persons involved to ensure realization of a technically sophisticated and producible device. The responsible person for this last step is Frank Unkrig: "This creative phase produces a prototype that is tested for its operability on a laboratory bench", the head of the test field explained. "This prototype is passed to me and I check whether the device proves when it reaches the limits of its performance capability and can be produced effectively.” To put it in a nutshell: During this phase of "follow-up development" the prototype is made ready for series production.”
That means: Frank Unkrig receives the prototype, i.e. the equipped boards and the mechanical parts. The series device is mounted from these parts in such a way that it can be produced as easy a possible. "The main task is to optimize the parts lists to ensure that the amount of different parts used for the device is as small as possible", Frank Unkrig explains. "One example is that the colleagues in the development department often use a multitude of different screws. My job is to reduce the types of screw models to a minimum." Furthermore, Frank Unkrig cares for safe packing and efficient shipping of the devices. "The packing was a major challenge for the EST project, because the device is shipped to the customer without processor card. As a consequence I had to conceive an alternative packing to ensure safe shipping of the device."
Individual test equipment for tailor-made devices
For the so-called pilot series, Frank Unkrig makes modifications, which also have to be tested. These tests are done with individual test equipment built by SIEB & MEYER in parallel to the prototype development. "I approach the project at a very early stage and ask for parameters as voltage, volume and measuring system of the device", Frank Unkrig explained. "On this basis, I design the test equipment, which ist, however, a collaboration project: Sometimes, the development builds parts of the test equipment or writes software required for testing a specific product." As the products are individual devices with different types of construction the appropriate test equipment is also unique and ranges from small appliances with a weight of only a few grams to cabinets with the size of a small room. The circuit of the power electronics is tested as well as the load capacity of the devices when they reach the limit of their performance capability – that means at 15 % overvoltage and a rated temperature increased by about 10 degrees.
Of course, the efficiency has a high priority in this field – therefore Frank Unkrig tries to conceive test equipment that can be used for testing several devices. Especially with successor models like at EST this is usually possible with some adjustments and extensions. The test equipment usually can be used after some adaptations and expansions has been done.
The moment when Frank Unkrig approves the prototype it will be aligned with the functional specification and the delivered to the customer who will run more function tests with the device. If improvements are made - which is rarely the case - SIEB & MEYER will consult with the customer until everything fits for both sides. "In the case of the EST project we carried out the initial operation with the new processor card in-house in Lueneburg and then delivered the prototype to the customer", Ralph Sawallisch remembered. "At EST extensive tests were done with the corresponding tightening tools." If the customer gives the go-ahead for the device, the technical documentation which has already been created in parallel to the development, is completed. Now, the series production can start: The project is finished and the customized device will prove in the following months and years in practice – as it is the case with the tailor-made SD2, used in EST controls of the newest generation.
"Customized development projects always confidence of both partners", Ralph Sawallisch finally emphasized. "If a customer orders a tailor-made device at SIEB & MEYER, he must be sure of the long-year availability of the device on the one hand. On the other hand, we have to trust our customers that they follow the described path with us to the end, regardless of possible obstacles that might occur." The conclusion is: Strong partners who can depend on each other will reach success.