Operating Machine Tools & Co. Safely Without Speed Sensors
Technical papers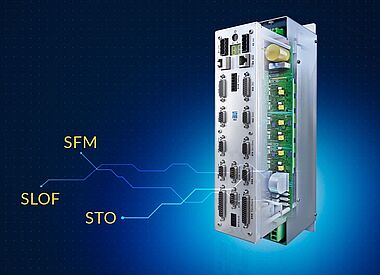
Safety Functions by SIEB & MEYER
Operators and service engineers of machining centers and machine tools are in danger of rotating tools, especially when rotating axes are involved. In order to ensure safe operation and protection against injury, legislators issued the Machinery Directive, which is binding for manufacturers. SIEB & MEYER provides the machine manufacturers with two sensorless safety functions SFM and SLOF. These are implemented in the drive controller SD2 and can monitor both the rotating field and the standstill. The outcome is a functional and cost-effective solution.
Operators and service engineers of machining centers and machine tools are in danger of rotating tools, especially when rotating axes are involved. In order to ensure safe operation and protection against injury, legislators issued the Machinery Directive, which is binding for manufacturers. SIEB & MEYER provides the machine manufacturers with two sensorless safety functions SFM and SLOF. These are implemented in the drive controller SD2 and can monitor both the rotating field and the standstill. The outcome is a functional and cost-effective solution.
Spindles and motors do not have to be equipped with speed sensors for safe speed monitoring: This is especially of relevance for applications such as high-speed cutting or high-speed grinding, where speed sensors are omitted due to spatial or financial reasons. "The challenge for the machine manufacturer is implementing the aspects personal safety and productivity at the same time and in the best possible way, and to implement them in accordance with the regulations," explained Markus Finselberger, Key Account Manager Drive Technology at SIEB & MEYER. "Typical safety solutions for motors and spindles require secure speed sensors, in order to determine or prevent dangerous operational states." These speed sensors are in their turn evaluated by special safety components. Both the speed sensors and the monitoring devices are additional components of the machine or of the switch cabinet, which require space, pose a risk of failure, must be maintained, installed and not least also paid for. Alternatively, machine manufacturers can also accept cutbacks in performance, e.g. if instead of measuring standstill, a certain waiting time is implemented before opening the door to ensure safety.
Reducing the risk of injury for operators
Specifically, the end customer is provided with the following two certified safety functions: Safe Frequency Monitor (SFM) and Safe Limited Output Frequency (SLOF). Both have been certified by TÜV Nord according to EN61508:2010, meeting the requirements of the safety integrity level of SIL3. The special feature of these two functions is that additional speed sensors are not required at the spindles
By means of the safety function SFM, the drive controller SD2 can safely detect whether or not the speed of a sensorless spindle has reached standstill or dropped below a safe speed value after switch-off. As long as this is not the case, a protective door, for example, remains closed. This safety function is used for rotating axes like grinding and routing spindles. The safety function SFM measures the rotating field of the motor and hence, enables a precise statement of the mechanical rotating field. The speeds or rotating field frequencies defined as safe result from the risk assessment of the machine carried out in accordance to the Machinery Directive
The SFM function is based on a frequency-dependent voltage that is induced by the motor or the remanence. This voltage can be measured at the motor terminals, regardless of whether a synchronous or an asynchronous motor is used. The drive determines the current rotating field frequency from that voltage and compares it with the parameterized limit value. If the rotating field frequency is within the parameterized range, the drive generates the status signal "Standstill" (safe standstill).
Avoiding critical speeds
The safety function SLOF is used to make sure that critical speeds are not exceeded. This can protect persons and equipment, for example, when a tool might break due to overspeed. For this purpose, the function determines the current rotating field frequency generated by the frequency converter and compares it with the parameterized limit value. If the limit value is exceeded, the output stage is disabled via the function STO. The system stops generating torque and thus acceleration, so that the spindle coasts down
Hence, the SLOF function allows to define a safe limit for the rotating field of a spindle. This prevents the drive from actively accelerating the connected spindle to a frequency that is too high. However, when an external system actively accelerates the spindle, the function cannot prevent exceeding the limit frequency (e.g. generator operation). If the safely parameterized maximum rotating field frequency is exceeded by, e.g. a wrong input, the function STO disables the output stage.
Load indicator included
Last but not least, a load indicator is integrated in all frequency converters and servo drivesof the series SD2x and SD4x. The indicator evaluates the torque-forming current of the motor and thus can be used to replace acoustic emission sensors. Hence, load changes of the motor are determined very precisely. This, in turn, allows drawing conclusions on possible tool breakage or tool wear. Additionally, the load indicator can detect the contact between tool and work piece (gap elimination). Furthermore, feed rates can be flexibly adjusted by using a load indicator
"In general, the safety functions provide a genuine added-value to the manufactures of machining centers or machining tools," concluded Markus Finselberger. "They prove themselves for instance in our customers' rotary transfer or grinding machines." The digital drive controller SD2 — especially designed for multi-axis systems, i.e. machines that use several processing spindles — makes a significant contribution and provides the operator with optimal protection thanks to its sensorless safety functions.