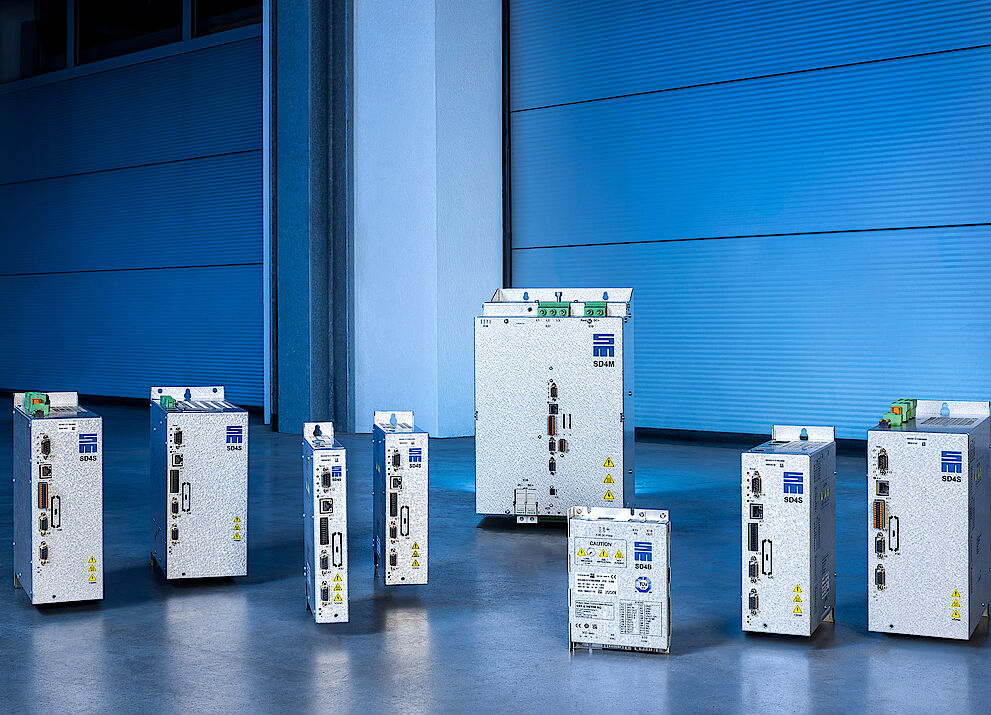
Technical papers
The Best of Two Worlds
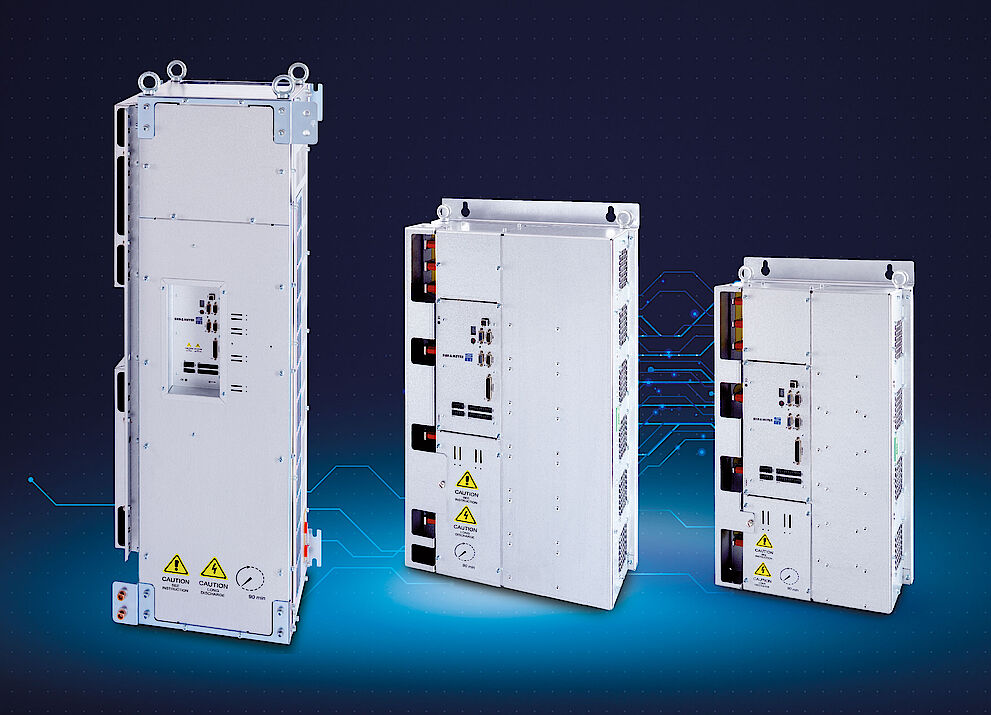
Technical papers
Minimal Motor Heating with High-speed Converters by SIEB & MEYER
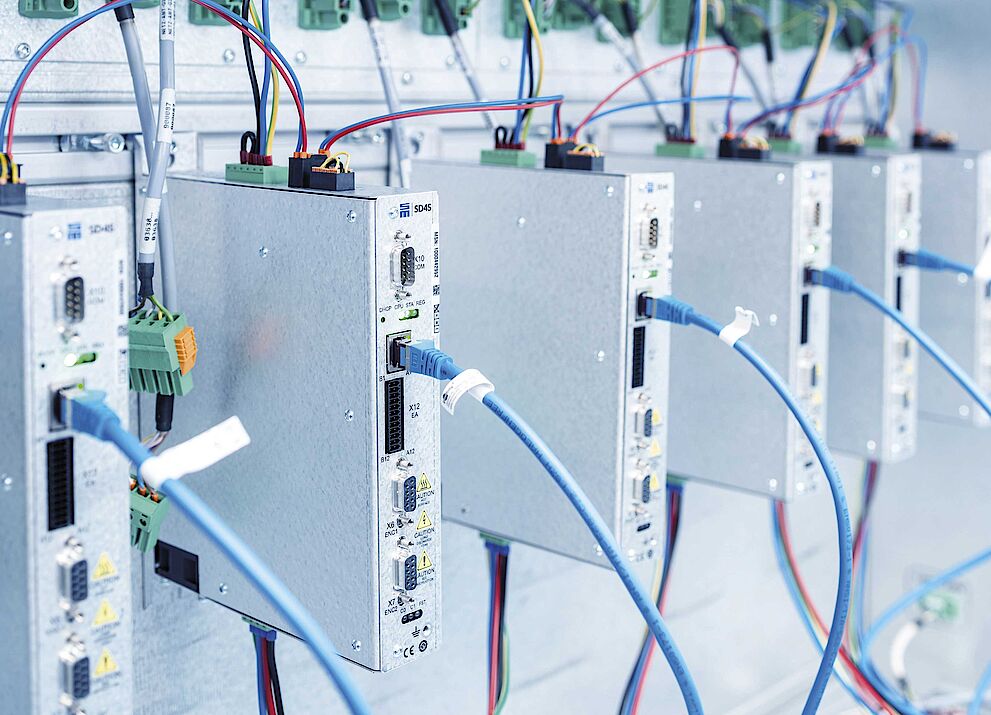
Technical papers
Screw Tightening with Straightforward Control
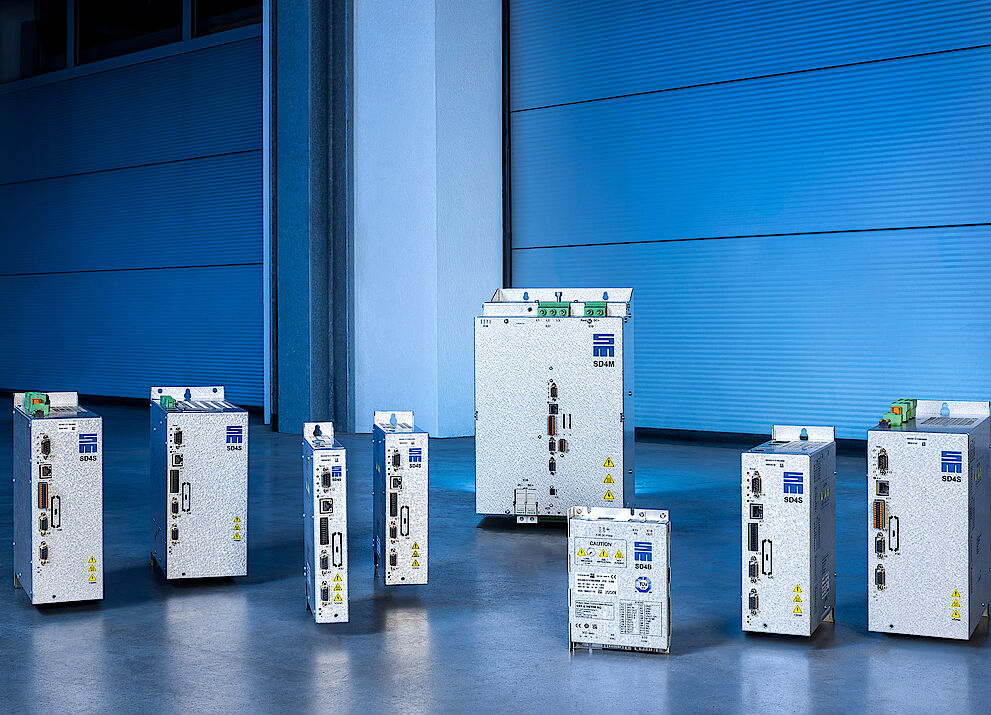
Technical papers
Frequency Converters Improve the Climate Footprint
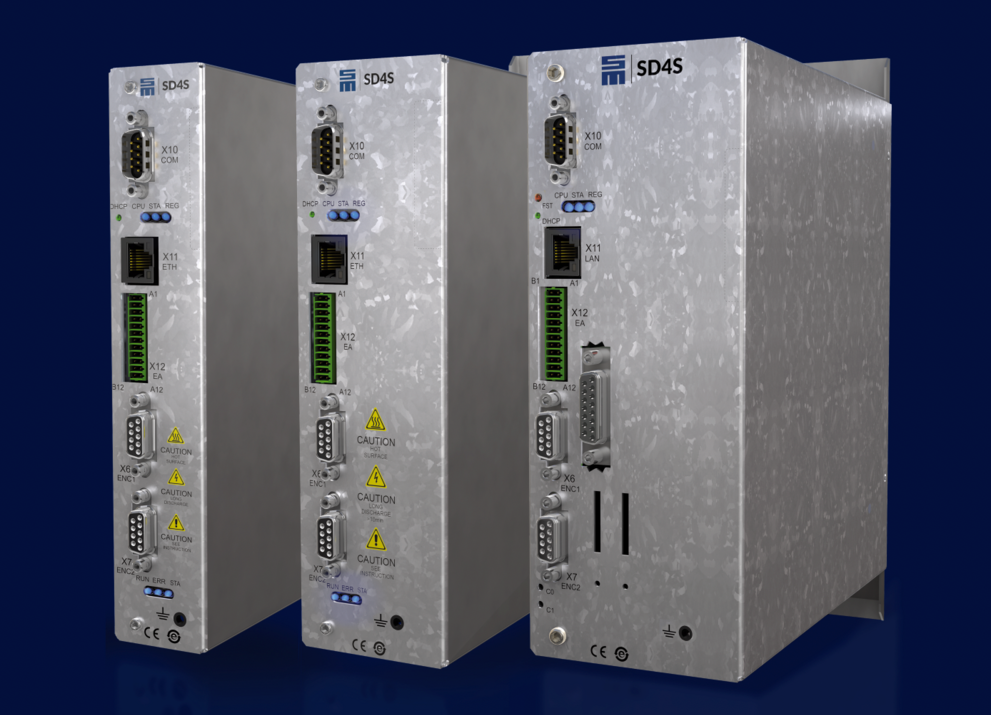
Technical papers
Optimal Operation of IPM Motors – with Frequency Converters of the SD4x Product Family
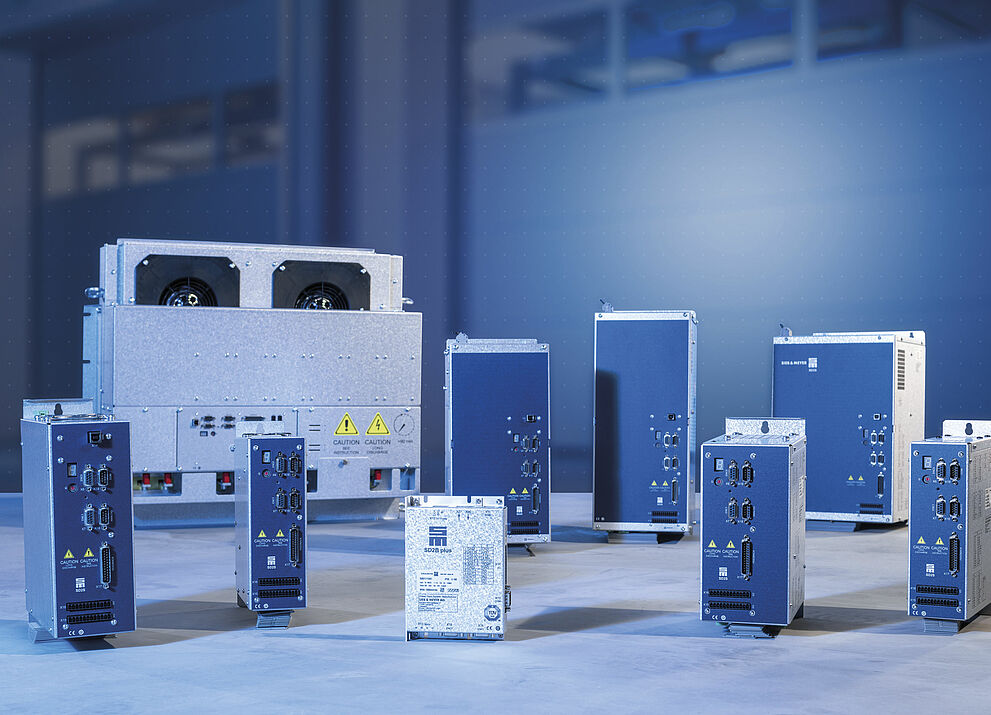
Technical papers
Frequency Converters: Past – Present – Future
DO YOU NEED MORE INFORMATION?
If you have any further questions, please do not hesitate to contact our press department:
Ms. Annika Ritari
PR, Media and Exhibitions
Phone +49-(0)4131-203 - 1381
E-Mail Annika.Ritari @sieb-meyer.de
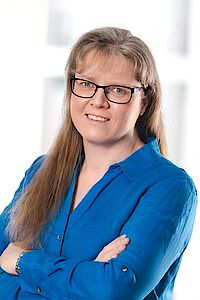